PRINCIPLE 3: Employee Wellbeing
- Please indicate the Total number of employees.
52,825 as at 31st March, 2016 (Includes Permanent, Temporary, trainee and contractual employees)
- Please indicate the Total number of employees hired on temporary/contractual/casual basis.
26,594 as at March 31, 2016
- Please indicate the Number of permanent women employees.
825 as at March 31, 2016
- Please indicate the Number of permanent employees with disabilities
18 as at 31st March, 2016
- Do you have an employee association that is recognized by management?
The manufacturing plants at Jamshedpur, Pune, Lucknow, Pantnagar and Sanand have employee unions recognized by the management. The Company enters into long term wage settlements with these recognized unions.
- What percentage of your permanent employees is members of this recognized employee association?
Around 98% of the operative employees at Jamshedpur, Pune, Lucknow, Pantnagar & Sanand plants are members of these employee unions. These employees represent 53% of the total permanent employees at these five Plants and 52% of the total permanent employees of Tata Motors. We do not have an Employees Union at our Dharwad Plant presently.
- Please indicate the Number of complaints relating to child labour, forced labour, involuntary labour, sexual harassment in the last financial year and pending, as on the end of the financial year
- What percentage of your under mentioned employees were given safety & skill up-gradation training in the last year?
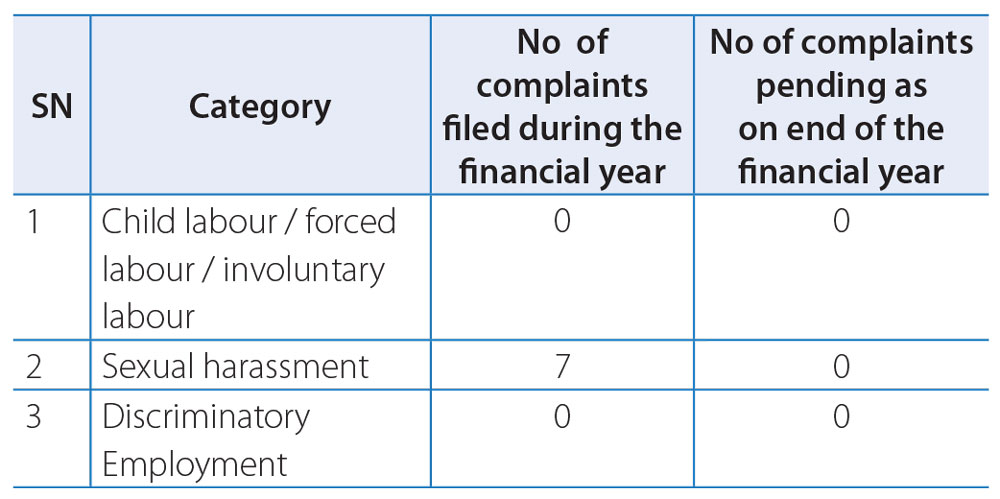
- Permanent Employees
- Permanent Women Employees
- Casual/Temporary/Contractual Employees
- Employees with Disabilities
Safety is of paramount importance to the Company. All employees at Tata Motors are provided with safety training as part of the induction programme. The safety induction programme is also a critical requirement for contract workforce before they are inducted into the system. The Company has a structured safety training agenda on an on-going basis to build a culture of safety across its workforce.
The Company believes in continual learning of its employees and has institutionalized a continual learning model for skill upgradation, especially at the shop-fl oor level. The learning and development needs of management cadre employees are met through the Company's L & D structure which includes various training delivery mechanisms.
PRINCIPLE 4: Stakeholder Engagement
- Has the company mapped its internal and external stakeholders?
Yes. The Company has mapped its internal and external stakeholders. It uses both formal and informal mechanisms to engage with various stakeholders to understand their concerns and expectations. Individual departments within the organization have roles and responsibilities identified and defined to engage with various stakeholders.
- Out of the above, has the company identified the disadvantaged, vulnerable & marginalized stakeholders?
Yes. The Company's AA policy is specially designed to address the socially disadvantaged sections of the society, Scheduled Castes and Tribes. Within the broader stakeholder group of communities, the Company works towards women empowerment and education of children. Every year, Tata Motors participate in TAAP (Tata Affirmative Action Program) Assessment, developed on the lines of TBEM (Tata Business Excellence Model). Tata Motors has been conferred the TAAP Jury Award for Fiscal 2015 and 2016.
- Are there any special initiatives taken by the company to engage with the disadvantaged, vulnerable and marginalized stakeholders. If so, provide details thereof, in about 50 words or so.
Our CSR programmes and projects are aimed at serving the needy, deserving, socio-economically backward and disadvantaged communities aimed at improving the quality of their lives. Under Tata Affirmative Action Programme (TAAP), the company continues to serve the SC and ST communities in inter alia Education, Employability and Entrepreneurship.
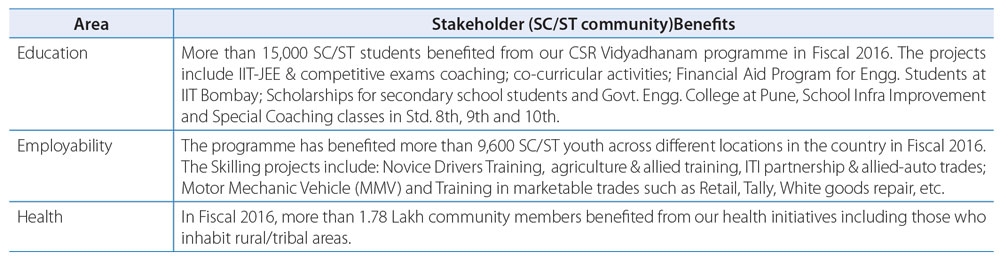
PRINCIPLE 5: Human Rights
- Does the policy of the company on human rights cover only the company or extend to the Group/Joint Ventures/Suppliers/Contractors/NGOs/Others?
Tata Motors respects human rights and has established a Policy on Human Rights. The policy details the Company's approach towards human rights and sets the Company's expectations of its Channel Partners and Contractors to adhere to principles of human rights. We encourage our suppliers, vendors, contractors and other business partners associated with the Company to follow the principles laid out in the Tata Code of Conduct.
- How many stakeholder complaints have been received in the past financial year and what percent was satisfactorily resolved by the management?
During the year, 50 concerns have been received towards actual or potential violation of Tata Code of Conduct, of which 44 of the complaints were satisfactorily resolved as on March 31, 2016
PRINCIPLE 6: Environmental
- Does the policy related to Principle 6 cover only the company or extends to the Group/Joint Ventures/Suppliers/Contractors/NGOs/others.
Sustainability is built into Tata Motor's business processes through well-defined Tata Group's Sustainability Policy. This policy reaffirms value system committed to social expenditure, environmental preservation and governance structure that engages employees and other stakeholders.
The Company also has Environmental Procurement Policy which is applicable to all its vendors, contractors and service providers.
- Does the company have strategies/initiatives to address global environmental issues such as climate change, global warming, etc.? Y/N. If yes, please give hyperlink for webpage etc
Yes. Tata Motors has adopted Tata Group's Climate Change policy to guide the organizational efforts towards mitigating and adapting to climate change. The Company approach towards climate change mitigation and pursuing low carbon growth is three-fold – develop cleaner and more fuel efficient vehicles, reduce environmental impacts of manufacturing operations and build awareness among stakeholders. It has also continually working on alternate fuel technologies like electric vehicles, hybrid vehicles and fuel cell technologies.
The Tata group became part of the Prime Minister's low carbon committee and was a member in the steering committee of the 'Caring for Climate' initiative of the United Nations Global Compact and United Nations Environment Programme. Ahead of the crucial global climate change talks that concluded in Paris, global corporate leaders signed an open letter on climate change, including Tata Sons Chairman Cyrus P Mistry.
- Does the company identify and assess potential environmental risks? Y/N
Yes. Tata Motors has an Environmental Policy which guides the Company's efforts to manage its environmental impacts and continually improve its environmental performance. All manufacturing plants in India are certified to ISO 14001 Environmental Management Systems (EMS) standard. As part of EMS implementation potential environmental risks are identified and appropriate mitigation strategies are planned.
- Does the company have any project related to Clean Development Mechanism? If so, provide details thereof, in about 50 words or so. Also, if Yes, whether any environmental compliance report is filed?
Tata Motors has own 'captive wind power' project of 21.95MW capacity. In Fiscal 2016 Pimpri Works utilized wind energy of 2.25 crores units (equivalent CO2e Reduction of 22,125 tCO2e), resulting into net savings of Rs. 8.9 Crores in electricity charges. Our Sanand plant utilized wind energy of 0.68 crores units (equivalent CO2e Reduction of 5,573 tCO2e) which was purchased through TPTCL, resulting into net savings of Rs. 0.478 Crores in electricity charges.
Renewable Energy Certificate (REC): Company's 21.95MW wind power project is registered under REC scheme. Cumulative 63,432 RECs generated; out of which 40,517 RECs sold through auction, resulting into cumulative benefit of Rs. 5.85 crores.
- Has the company undertaken any other initiatives on - clean technology, energy efficiency, renewable energy, etc. Y/N. If yes, please give hyperlink for web page etc.
The Company has always been conscious of the need for conservation of energy and has been sensitive in making progress towards this end. It also demonstrates its commitment to maximize the use of Renewable energy through its climate change policy. Not including its subsidiaries, Tata Motors currently sources around 8% of its electricity from renewables. Tata Motors has solar energy installations at three plants (Pune, Sanand, Dharwad ) of its manufacturing plants in India. It is also planning to source more renewable electricity from the grid in the future through open access agreement.
Recently Tata Motors Limited has joined the RE100 initiative of The Climate Group. Through this initiative, Tata Motors aspires to switch all manufacturing operations to 100% Renewable energy in the coming years.
Energy conservation measures have been implemented at all the plants and offices of the Company and special efforts are being put on undertaking specific energy conservation projects like:
1st roof top Solar PV Power Plant of 223 KWP has been commissioned at Pimpri Works on April 01, 2015. The generated solar power is utilized in the manufacturing process. Similar installation amounting to a total capacity of 1.8MWp capacity is being installed at Pimpri and Chikhali Works. Roof Top Solar PV Power Plant 1.8MWp has been installed & commissioned on Roof Top of Office Blocks at TATA MOTORS, Pune (CVBU & PVBU). Annual Solar Power Generation is 21.29 Lakh Kwh (equivalent CO2e Reduction of 2,097 tCO2e) for Fiscal 2016, resulted net saving of Rs. 0.59 Crores in electricity charges.
- Waste Heat Recovery System to recover waste heat from exhaust flue gases of Surfacer & Finish paint baking ovens, Conversion of Indirect fired baking ovens into Direct Fired Burner of baking ovens, Conversion of Electrical Heating into Natural Gas Heating system for washing machines
- Use of Energy Efficient 40W LED Batten fittings for Task lighting, 100W LED High bay for General Lighting, 19W LED Tube Lights in Office area, Installation of 42W LED street lights, Installation of 142W LED Flood Light fittings,
- Elimination of Pump operation by using gravity flow system, resizing of hydraulic power pack pump.
- Compressed Air Pressure optimization at Paint shop and at other shops, use of portable small compressors for low compressed air requirement on holidays, Installation of Shut Off Valves in compressed air network, downsizing of motors and delta to Star conversion of Motors.
- Installation of Variable Frequency Drives for various applications like Blowers, Pumps & Air supply plants.
- Use of Infrared sensors & timers for on-off control of Industrial fans, lighting system of Inspection Booths and Fresh Air blower operation. Modification in electrical logic for automatic switching on-off operation of hydraulic motors, coolant pumps, blowers etc., Optimization of AC plant operations.
These efforts have resulted in Electrical energy saving of 1.47 Crores units, Fuel saving – Light Diesel Oil 6 KL, LPG/Propane 586.32MT and Natural Gas 0.61Lakh SCM. The whole effort resulted in cost savings for the company of around Rs. 14.5 crores & annual CO2 emission reduction 13,960 tCO2e.
Please refer to the Annexures to the Directors' Report for energy efficiency initiatives.
- Are the Emissions/Waste generated by the company within the permissible limits given by CPCB/SPCB for the financial year being reported?
The Company is in compliance within the prescribed permissible limits as per CPCB/SPCB for air emissions, effluent quality and discharge, solid and hazardous waste generation and disposal.
- Number of show cause/legal notices received from CPCB/SPCB which are pending (i.e. not resolved to satisfaction) as on end of Financial Year.
There is no show cause/legal notice pending resolution by CPCB/SPCB