Particulars of Conservation of energy, Technology absorption and Foreign exchange earnings and outgo in terms of Section 217(1)(e) of the Companies Act, 1956 read with the Companies (Disclosure of particulars in the Report of Directors) Rules, 1988 forming part of the Directors' Report for the year ended March 31, 2014:
A. CONSERVATION OF ENERGY
The Company has always been conscious of the need for conservation of energy and has been sensitive in making progress towards this initiative. Various energy conservation measures have been taken at all the plants and offices of the Company to implement energy conservation projects like:
- Conversion of electrical heating into Natural Gas (NG) heating system of washing machines and tempering furnace, conversion of LPG heating into NG heating of Endogas generators, conversion of indirect heating into direct heating system for ovens in Paint Shop, reduction in surface heat loss, improvement in burning efficiency of burners by controlling the air - fuel ratio with the help of flue gas analysis, optimization of Paint shops oven as per production schedule.
- Installation of LED Tube lights, LED street lights, LED low bays fittings, LED bus bar indicators. Installation of energy savers in lighting circuits, switching OFF unwanted lights, installation of Star rated Air Conditioning systems, etc.
- Installation of Variable Frequency Drives for various applications like Blowers, Pumps and Air supply plants as a flow control strategy for energy conservation.
- Fresh Air blowers replaced by Man cooler fans, automation for Blower operation, use of motion sensors and timers for ON-Off control of lighting system, blowers and fans.
- Optimization of compressed air supply pressure, use of DC powered nut runners in place of Pneumatic nut runners, use of pressure control valves and Isolation valves in compressed air network, localized small compressors for low pressure requirement, migration of localized dryer system to centralized dryer system for dry compressed air supply.
- Modification in electrical logic for automatic switching On-Off operation of hydraulic motors, coolant pumps, blowers etc, optimization of AC plant operations, removal of unwanted AC systems.
- Wind Ventilators, downsizing of motors, trimming of impellers of oversized water recirculation pumps, Delta to Star connection of motors etc.
All these efforts have resulted in saving of electrical energy of Rs.2.67 crores units, Fuel saving: Diesel - 39.7KL, LPG/Propane - 209MT and Natural Gas - 1.66 Lakh SCM. The whole effort resulted in cost savings of around Rs.20.28 crores and annual Co2 reduction 22,938 tCo2e.
Company has taken new initiative for implementation of ISO: 50001 Energy Management System (EnMS) across all the Company's Plants in India. The Company's Pune, Jamshedpur, Lucknow, Pantnagar, Sanand and Dharwad Plants are certified for ISO: 50001 Energy Management System (EnMS) by M/s BVC.
Company's endeavor for maximizing use of wind energy (Green Power) has also made significant contributions.
- In addition to the Company's own ‘captive wind power' projects of 21.95 MW capacity, further initiatives have been taken to purchase wind power from ‘Third Party wind developers' through open access. For this, PPAs signed for purchase of additional wind power of Rs.8.80 crores Wind units with five parties. With this, Company's CVBU Pimpri Plant's total Wind Power utilization for FY 2013-14 reached to Rs.9.07 crores wind units (equivalent Co2e Reduction of 84,931 tCo2e), this resulted in net savings in electricity charges of Rs.27.14 crores.
- Renewable Energy Certificate (REC): Company's 21.95MW Wind Power project is registered under REC scheme. Cumulative 32,544 RECs generated; out of which 18,931 RECs sold through auction, cumulative benefit of Rs.2.72 crores.
Award / Recognition received during the year is as below,
- CVBU Pune Plant is honored with "Excellent Energy Efficient Unit Award" by CII-National award for Excellence in Energy Management - 2013, under Automobile Manufacturing category.
B. RESEARCH AND DEVELOPMENT
Specific areas in which R & D carried out by the Company
The Company's R&D is aligned towards developing and acquiring the technology, core competence and skill sets required for robust and timely delivery of the envisaged future product portfolio with leading product attributes across the range of commercial and passenger vehicles. For the passenger vehicle product range, the focus is on stunning design, driving pleasure and connected car technologies and for the commercial vehicle product range the focus is to be the market leaders by enhancing fuel efficiency and minimizing total cost of ownership.
All the R&D activities that the Company is currently undertaking takes into account the current and likely future regulatory norms along with meeting and exceeding the prescribed and prevalent vehicle safety regulations. The company also continues its R&D efforts in developing vehicles which are powered by alternate fuels like CNG, LPG, Bio-diesel, electric traction and Hydrogen some of which was showcased at the Delhi Auto Expo in February 2014 as well.
Benefits derived as a result of the above R&D
The Company maintains requisite R&D facilities, core competence and skill sets enabling it for compliance of regulations and reducing product development time to meet market requirements. Increasing use of ‘digital validation' techniques has enabled a reduction in the number of physical prototypes required. All existing Company products and engines are compliant with the prevalent regulatory norms.
During the FY 2013-14, the Company filed 73 Patent Applications and 157 Design applications. In respect of applications filed in earlier years, 18 Patents were granted and 20 Designs were registered.
Future Plan of Action
The Company continues its effort on developing new products and technologies to meet growing customer expectations. The existing products will be refreshed at regular intervals to suit upcoming trends. In the long term, the Company is focusing on improving driving comfort, fuel efficiency, performance and design aesthetics. Company's R&D is also committed to minimize the environmental impact and carbon footprint of its products and manufacturing operations, with Greenhouse Gas (GHG) emissions in particular. The Company is uniquely placed to meet this commitment, with its comprehensive product line-up and indigenous manufacturing base.
Expenditure on R & D
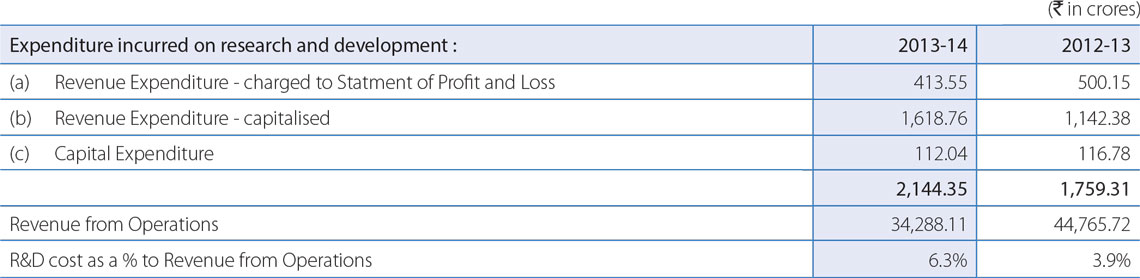
C. TECHNOLOGY ABSORPTION, ADAPTATION AND INNOVATION
Efforts made towards technology absorption, adaptation and innovation
The Company is putting continuous efforts in acquisition, development, assimilation and utilization of technological knowledge through its wide advance engineering project portfolio. The projects in the advance engineering portfolio are focused around the technologies and innovations which the Company might need in the years to come and the current thrust areas being automotive applications like light weighting, fuel efficiency improvement and Hybridization with alternate fuel like CNG, LPG, Ethanol, bio-diesel, electric traction, Hydrogen etc. The Company is actively working on various hybrid and electric power trains for hybrid, electric and fuel cell electric vehicles for both commercial and passenger car applications and making good progress.
The Company took initiatives by various interventions at Powertrain and vehicle level to improve upon the performance, refinement, meeting and exceeding the current prevalent norms of emission, fuel economy and reduction in carbon footprint of the products launched recently as well as the future products and platforms. The Company continues to work on the already initiated new generation powertrain programmes which would meet the stringent future domestic and international emission norms. As a longer term action, the Company has also started taking into cognizance the current CAFÉ (Corporate Average Fuel Economy) and what would the likely future regulations entail on the envisaged future product portfolio.
The Company is also currently focusing on bringing safer vehicles to the end customers and the vehicle occupants (both active and passive safety) than the norms currently prescribed for which extensive safety attribute target setting, Computer-Aided Engineering, Simulation and testing capabilities has been baked into plan for delivering the future products on the anvil.
The Company is progressing well in its innovative and constant endeavour to front load the future product development process with concurrent engineering, digital validations and upfront failure mode identification. All relevant development and testing facilities and infrastructure required to support the endeavour like state-of-the-art advanced design studio, rapid proto-type development system, testing cycle simulators, advanced emission test laboratories are being put in place to support this migration of heavier digital product development model.